Master a number of independent research and development core technologies, and is committed to the corrugated packaging industry towards the whole plant intelligence
500mm cutting length, 200m/min
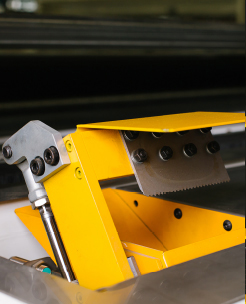
Auto edge cut
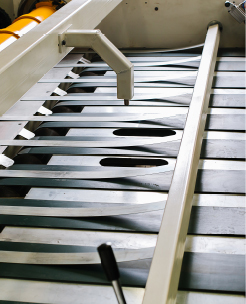
No paper detect
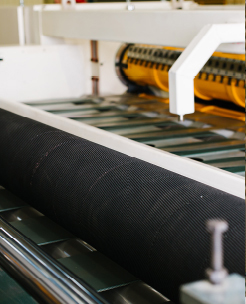
Synchronized paper convey
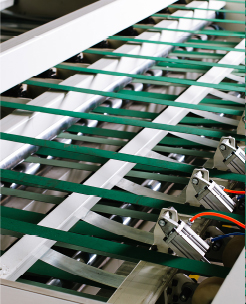
Press wheel auto lift
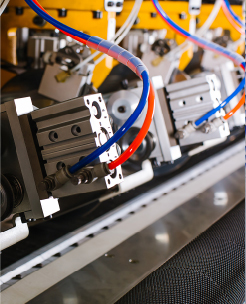
Auto lubrication
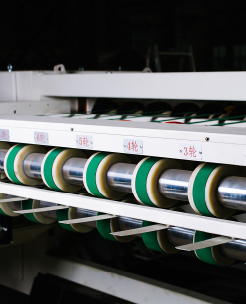
Two belts paper ejection
- 01 1 PLY Full auto thin knife slitter
- 02 1 PLY Full auto cross cutter
- 03 1 PLY Full auto stacker
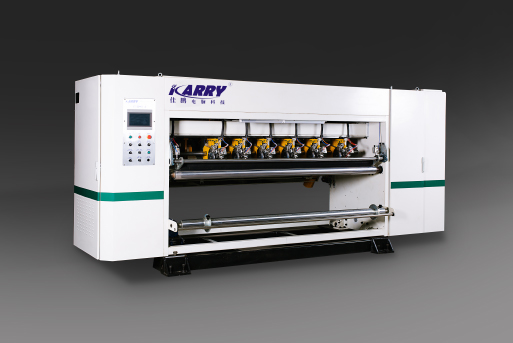
Each knife in the longitudinal cutting process is independently servo-controlled, providing you with higher changeover efficiency.
The combination of splined shaft and synchronous belt.
The knives are made of large diameter, high toughness, and high-strength hard alloy
Enabling electric automatic correction to solve the problem of misalignment caused by improper paper feeding in the single-sided machine.
Driven by a permanent magnet synchronous servo motor, ensuring accuracy and reliability, achieve a single-sheet change in 1 second
The speed of the slitter cutter is controlled by servo control, automatically adjusting to synchronize with the sheet speed.
The automatic edge-cutting system automatically cuts off the paper edges during order change.
Equipped with 10 inches industrial pad
Equipped with industrial air-conditioner, the devices work in a dust-free, constant temperature and humidity situation.
Connected to production management system for automatic multi-functional cutting, equipped with standard communication and control interface
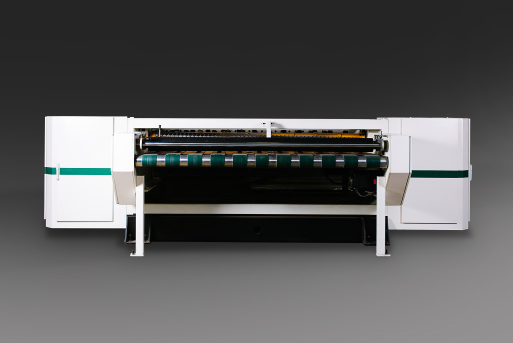
With the addition of alloy steel seamless steel pipe spiral knife shaft, the production efficiency of short paperboard is greatly improved.
Traction section adopts belt conveyance
The traction section is designed with an open design for easy installation, maintenance, and shorter downtime for paper jam handling
Traction speed is servo-controlled with a constant tension control mode and equipped with a professional PID tension algorithm.
Cross-cutting section is driven by an independent servo motor to improve cutting precision.
The upper and lower blades in the cross-cutting section have a sawtooth shape.
The frame structure is modular in design with precise processing, ensuring long-term stable operation.
The alloy steel helical cutter shaft has low inertia and high rigidity.
Automatic lubrication system
Paper output is servo-controlled
Paper output section is equipped with a power brush
paper output section has an automatic control pneumatic lifting pressure wheel device Automatic order change, with an optional automatic paper joints trimming function
Equipped with industrial air-conditioner, the devices work in a dust-free, constant temperature and humidity situation.
Connected to production management system for automatic multi-functional cutting, equipped with standard communication and control interface
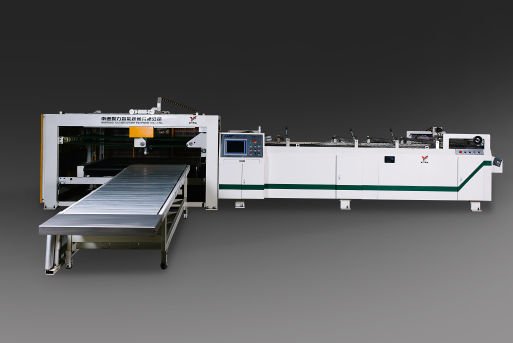
The stacking machine is fully servo-controlled and uses high-strength synchronous belts and conveyor belts to ensure stacking efficiency.
- Four conveying belt, line speeds with overall planning (rated line speed can meet the line configuration standard when the paper meets the requirements):
- A paper exit pressure wheel device at the end of the conveying section to prevent paper flipping caused by sudden acceleration
- The first section uses a full-width conveyor belt, while the rest uses multiple narrow conveyor belts for conveying(to prevent paper from falling )
- The stacking conveyor section is equipped with a pressure plate adjustment device to adjust the position and angle of the pressure plate.
- Belt control is servo-controlled, follows the line speed
- An additional round belt is added above the platform to extend the conveying section, facilitating the conveying of long cardboard.
- The latter baffle is equipped with collecting belts that rotate at high speed to position the paper
- The stacking platform adopts a balanced counterweight method
- The movable counter paper adopts a fully automatic servo adjustment system
- The latter baffle is servo-controlled
- The paper arranging is servo-controlled and automatically adjusted based on the line speed
- The basket is servo-controlled.
- The cross conveying control is servo-controlled, ensuring smooth paper output
- Standard communication interfaces and control interfaces are available to integrate with Equipped with industrial air-conditioner, the devices work in a dust-free, constant temperature and humidity situation.
- Connected to production management system for automatic multi-functional cutting, equipped with standard communication and control interface
Device parameters
- Specification
- JPNCDW2500
- Effective cutting width
- 1800﹑2200﹑2500﹑2800﹑3100﹑3300
- Minimum cutting width
- 160mm
- Transmission method
- Adopted gear rack transmission
- Cutting length
- 350-2000mm(or customized according to customer needs)
- Cutting thickness
- 8mm
- Order quantity
- N sets of orders, which can be switched without stopping the machine
- Longitudinal cutting accuracy
- ·
- Transverse cutting accuracy
- ·
- SCADA
- Industrial touchscreen or tablet
- PLC
- Schneider Electric series
- Transverse main drive
- British CT servo drive
- Servo drive
- Schneider Electric
- Low-voltage electrical equipment
- Schneider series
- Feeding section traction motor
- 1 servo motor
- Cut Drive Motor
- 1 servo motor
- Waste Suction Motor
- 1 servo motor
- Sorting Positioning Motor
- 14 Servo Motors (Based on the Specific Number of Blades Ordered)
- Cross-Cutting Drive Unit
- 2 servo motor
- Paper Feeding Drive Motor
- 1 servo motor
- Paper Discharging Drive Motor
- 1 servo motor
- Paper Depth Adjustment Motor
- 1 servo motor
- First and Second Stage Conveying Motor
- 2 servo motor
- Third and Fourth Stage Conveying Motor
- 2 servo motor
- Basket Hoist Motor
- 1 servo motor
- Platform Paper Ejection Motor
- 1 servo motor
- Barrier Movement Motor
- 1 servo motor
- Pulley Motor
- 1 servo motor
- Press Adjustment Motor
- 2 servo motor